A contaminação do leite e dos produtos lácteos podem iniciar com a obtenção da matéria-prima inviável ou contaminada e pode se estender às etapas de processamento, transporte, recepção e armazenamento, ou seja, a produção primária. Sendo assim, eis a pergunta: como mapear os pontos de riscos de contaminação na cadeia de laticínios?
Já na produção primária que iniciam os problemas com contaminações, onde estas falhas podem provocar danos e perdas em lotes, problemas de saúde pública, imagem institucional danificada e outros problemas que poderiam ser evitados.
Para evitar esses problemas, é necessário adotar medidas de controle nas diversas etapas da cadeia produtiva de lácteos, com o intuito de diminuir as contaminações e, consequentemente, os surtos por doenças transmitidas por alimentos (DTAs).
A adoção dessas medidas pode ser feita por meio da análise de riscos e da implantação de ferramentas da qualidade.
Para a análise de riscos, especificamente, há diversas ferramentas de gestão utilizadas e que podem auxiliar no controle de processos e produtos:
- Análise de modos de falha e efeitos (FMEA);
- Análise de modos de falha, efeitos e criticidade (FMECA);
- Análise da árvore de falhas (AAF);
- Análise de perigos e operabilidade (HAZOP);
- Análise preliminar de riscos (APR);
- Sete ferramentas da qualidade;
- Análise de perigos e pontos críticos de controle (APPCC), sendo esta a mais utilizada em função do amparo legal através de legislações que implantaram a metodologia gradativamente em todas as indústrias de produtos de origem animal.
- Além de normas e sistemas da qualidade tais como a ISO 22000 e FSSC 22000.
Para a efetiva análise de riscos, é necessário a aplicação de programas de pré-requisitos aplicados a qualquer segmento da indústria de alimentos, assim como a de laticínios, tais como, as boas práticas de fabricação (BPF), procedimentos operacionais padronizados (POP), programa de pré-requisitos operacional (PPRO), programas de autocontrole (PAC), procedimentos padrão de higiene operacional (PPHO) e avaliação de riscos (ARM) e monitoramentos microbiológicos.
Os programas de pré-requisitos constituem a primeira etapa para assegurar a qualidade dos alimentos nas indústrias e, também, auxiliam na redução de custos e na definição de controles operacionais (CARBONERA, 2007). Além das abordagens mais tradicionais, alguns laticínios vêm implementando novas metodologias para mapear os pontos de riscos como o monitoramento microbiológico utilizando sequenciamento de DNA.
Análise de riscos microbiológicos
A análise de pontos de riscos, que teve seu desenvolvimento inicial para a área militar, e que foi adapatado para todos os segmentos industriais e atividades, e também, é utilizada para a gestão da segurança dos alimentos, visto que:
- Instrumentaliza os processos de tomada de decisão;
- Contribui para a definição de metas e de estratégias para a redução da ocorrência das DTAs e das doenças transmitidas pela água;
- Planeja e implementa as intervenções adequadas;
- Monitora os resultados (DUBUGRAS; PÉREZ-GUTIÉRREZ, 2008; VIANA, 2011; CARVALHO, 2012). A análise de risco utiliza uma abordagem científica com caráter multidisciplinar para reconhecer e quantificar as relações entre os agentes de riscos e os danos, e corroborar as alternativas, para mitigar ou aceitar os riscos (VIEIRA, 2009; FIGUEIREDO; MIRANDA, 2011).
A análise de risco é realizada em três etapas: avaliação, gerenciamento e comunicação de riscos (CODEX ALIMENTARIUS, 2015).
Etapa 1 – Avaliação de riscos
Primeiro, é necessário conhecer os perigos. Conhecer os microrganismos é um ponto vital nessa etapa do processo. Os perigos encontrados em alimentos podem ser de três tipos: físicos (fragmentos de objetos como vidro, metal, madeira); químicos (pesticidas, solventes, antibióticos, desinfetantes, entre outros); e biológicos (bactérias patogênicas, parasitas, fungos, toxinas) (REIS, 2001; CARBONERA, 2007; FDA, 2007; HILBIG, 2012).
Cada perigo em potencial, que for identificado na planta, deve ser avaliado quanto à probabilidade da sua ocorrência e as consequências da severidade dele para a saúde, o que é denominado risco.
Dessa forma, podem ser classificados em alto risco, quando tem um impacto grave e agudo na saúde pública, mesmo com baixa frequência de ocorrência; e moderado risco, o qual pode ser controlado com BPF e PPHO (FDA, 2007).
A avaliação de riscos tem como base: os conhecimentos científicos sobre os perigos e riscos presentes na cadeia produtiva; a avaliação qualitativa e/ou quantitativa da natureza dos efeitos adversos à saúde causados pelos perigos encontrados nos alimentos; a avaliação qualitativa e/ou quantitativa da provável ingestão de agentes biológicos, químicos e físicos contidos em alimentos; a avaliação da dose-resposta; e a estimativa de grupos vulneráveis ou expostos a alto risco (FAZIL, 2005; VIEIRA, 2009; FIGUEIREDO; MIRANDA, 2011).
Etapa 2 – Gerenciamento de riscos
Essa etapa trata do processo de decisão, o qual deve ponderar os fatores econômicos, a viabilidade técnica, política e econômica, as incertezas, entre outros. Se necessário, é feita a seleção e a aplicação de medidas de prevenção e controle de problemas, baseadas nas conclusões da avaliação de risco (FAZIL, 2005; VIEIRA, 2009; FIGUEIREDO; MIRANDA, 2011).
Etapa 3 – Comunicação de riscos
Na etapa de comunicação é divulgado o que acontece durante todas as fases do processo de análise de risco às partes interessadas internas e externas. O plano de comunicação deve ser desenvolvido já no início da análise de riscos e convêm que aborde questões relacionadas às suas causas, consequências, resultados da avaliação e as decisões do gerenciamento (FAZIL, 2005; VIANA, 2011).
Definição de pontos de riscos: quais as ferramentas disponíveis?
Abaixo, a definição de algumas ferramantas estatísticas, gráficos e fluxogramas que auxiliam na identificação das principais causas de falhas no processo produtivo em laticínios. Vamos estudar as 5 ferramentas mais utilizadas na cadeia de laticínios:
1. As “sete ferramentas da qualidade”:
1. Folha de verificação: é uma planilha ou formulário para o registro de dados. Os itens a serem verificados são definidos e impressos em uma folha, de modo que os dados possam ser coletados de forma fácil e concisa. Posteriormente, os dados coletados são analisados. Essa ferramenta permite uma rápida percepção da realidade e uma imediata interpretação da situação, auxiliando na redução de erros. As vantagens são que torna simples e fácil a coleta de dados e ajuda no planejamento das melhorias. As desvantagens são que exige um planejamento cuidadoso, tanto para definir os itens relevantes a serem verificados como para exibir os resultados, e o processo de coleta de dados pode ser lento e demandar recursos.
2. Estratificação: consiste na divisão de um grupo em diversos subgrupos com base em suas características semelhantes. Tem como objetivo identificar como a variação de cada fator pode afetar o resultado do processo ou problema. As suas vantagens são que ajuda a detectar um problema e onde ele ocorre, e verifica o impacto de uma determinada causa sobre o efeito em estudo. Já como desvantagem é que se pode estratificar muito ou pouco, perdendo a possibilidade de obter informações relevantes.
3. Diagrama de Pareto: é um gráfico de barras verticais que dispõe a informação de forma a tornar evidente quais são as prioridades, apresentando-as de maneira que permita a concentração dos esforços para a melhoria dessas áreas. As suas vantagens são que permite a visualização dos diversos elementos de um problema, ajudando a classificá-los e priorizá-los, e facilita o direcionamento de esforços. Como desvantagens: existe a tendência de deixar os riscos menos significativos em segundo plano; não é uma ferramenta de fácil aplicação; nem sempre a causa que provoca não-conformidade, mas cujo custo de reparo seja pequeno, será aquela a ser priorizada.
4. Diagrama de Causa-E-feito (Diagrama de Ishikawa): é utilizado para identificar quais as causas que ocasionam determinado efeito. Cada causa é estudada de forma individual e específica, aumentando assim a visão do problema, enriquecendo a sua análise e tornando-o mais fácil de solucionar. Tem como vantagem o fato de ser uma ferramenta estruturada e que permite ter uma visão ampla de todas as variáveis que interferem no bom andamento da atividade, ajudando a identificar a não-conformidade. As desvantagens são: é limitada à solução de um problema por aplicação; não apresenta quadro evolutivo ou comparativo histórico, como é o caso do histograma; e para cada nova situação, é necessário percorrer todos os passos do processo, utilizando o diagrama.
5. Histograma: tem a função de descrever as frequências com que variam os processos. É uma representação gráfica dos dados obtidos por meio de observação. As vantagens dessa ferramenta são a sua elaboração rápida e o modo como facilita a solução de problemas, principalmente quando se identifica numa série história a evolução e a tendência de um determinado processo. Já as desvantagens são que fica ilegível quando é necessária a comparação de muitas sequências ao mesmo tempo e, para um grupo de informações, torna-se necessário a confecção de diversos gráficos para melhorar a compreensão dos dados.
6. Diagrama de Dispersão: consistem em técnicas gráficas utilizadas para visualizar e analisar as relações entre duas variáveis. Como desvantagens dessa ferramenta têm-se: é um método estatístico complexo, que necessita de conhecimento sobre a ferramenta para que possa utilizá-la; exige conhecimento do processo, cujo problema deseja-se solucionar; e não há garantia de causa-efeito.
7. Gráfico de Controle: é utilizado para monitorar os processos, devendo detectar a ocorrência de causas especiais e sinalizar aos analistas a necessidade de investigá-las e ajustá-las, conforme o tamanho dos desvios encontrados. Têm como vantagens: mostrar uma tendência, ao longo do tempo, de determinado processo; e apresentar dados estratificados em diversas categorias. As desvantagens são: tem que ser periodicamente atualizado; é genérico; e é necessário ter conhecimentos básicos de estatística para poder escolher o tipo de gráfico mais adequado para cada situação.
2. Mapeamento de processos (Business Process Management – BPM)
O mapeamento de processos permite listar o fluxo de atividades que permeiam a organização, seguindo a sua passagem por diversas áreas, departamentos e funções, nos quais podem ser identificados gargalos e duplicidade de atividades.
Há várias técnicas para a realização do mapeamento, entretanto, o fluxograma é o mais utilizado.
Essa ferramenta tem como vantagens: aplicação em processos simples e complexos; auxilia na localização de falhas; permite a melhoria contínua; e permite fácil compreensão do processo (HÖRBE et al., 2015).
O fluxograma consiste em um resumo ilustrativo, em etapas, das várias operações de um processo.
Essa ferramenta é fundamental para o planejamento (elaboração do processo) e para o aperfeiçoamento do processo, uma vez que facilita a visualização das suas diversas etapas e permite identificar os pontos de riscos que merecem atenção especial por parte da equipe de melhoria (RENO, 2015).
3. Análise Preliminar de Riscos (APR)
A análise preliminar de riscos (APR) é utilizada para reconhecer, analisar e gerenciar riscos. Essa ferramenta requer a formação de equipes multidisciplinares, com a presença de profissionais, com diversidade de experiências, e de especialistas.
A equipe busca, a partir da troca de informações sobre suas vivências, estabelecer consensos em relação aos riscos envolvidos em cada atividade ou tarefa e recomendar a adoção de medidas que venham a prevenir a ocorrência de situações indesejadas (BARRETO; MEIRIÑO, 2016).
A APR geralmente é aplicada na fase de projeto das instalações, quando não se possui maiores informações sobre os riscos, e é uma técnica baseada em pesquisas bibliográficas e conhecimentos científicos.
Em uma ficha são explicitadas as variáveis básicas: “Risco”, “Causa”, “Consequência/Efeito”, “Categoria do risco” e “Medidas preventivas/corretivas”, onde medidas de controle já existentes são consideradas (SELLA, 2014).
A APR tem as vantagens:
- É sistemática e lógica;
- Identifica os perigos/riscos com antecedência;
- Identifica os critérios para dar continuidade ao processo;
- Ajuda na seleção de áreas da instalação nas quais outras técnicas de análise de risco devam ser utilizadas;
- Estimula o brainstorming;
- Tem aplicação relativamente rápida.
E as desvantagens são:
- A dependência da experiência do grupo participante
- Normalmente é aplicada na fase inicial, quando as informações disponíveis sobre o processo são limitadas (SELLA, 2014).
4. Análise de perigos e operabilidade (HAZOP)
A análise de perigos e operabilidade (HAZOP) é uma técnica qualitativa desenvolvida para examinar as linhas de processo, detectando os perigos e prevenindo os problemas.
É uma ferramenta especialmente indicada quando da implantação de novos processos, na fase de projeto, ou na modificação de processos existentes (KLETZ, 2001; CRAWLEY et al., 2008).
A análise é realizada através do emprego de palavras-chave que guiam o raciocínio da equipe, fixando a atenção nos perigos mais significativos do sistema.
As palavras-chave são aplicadas às variáveis identificadas no processo como pressão, temperatura, tempo, pH, entre outras, gerando os desvios, que nada mais são do que os perigos a serem examinados.
Essa técnica utiliza a imaginaçao dos integrantes do grupo para analisar os modos pelos quais um evento indesejado ou problema operacional possa ocorrer (KLETZ, 2001; CRAWLEY et al., 2008).
O HAZOP tem como vantagens:
- é sistemático e lógico;
- identifica os desvios que possam ocasionar eventos perigosos ou problemas operacionais;
- investiga as causas que podem gerar desvios no processo;
- estimula o brainstorming;
- melhora a eficiência da planta.
As desvantagens são a dependência da experiência do grupo participante, as medidas excessivas de proteção que podem ser adotadas a demora do processo (SELLA, 2014).
5. Sistema APPCC
O APPCC consiste em sete etapas, basicamente:
- Realizar a análise dos perigos e apontar medidas preventivas para cada etapa do processo;
- Identificar os PCCs;
- Estabelecer os limites críticos associados a cada PCC;
- Estabelecer o sistema de monitoramento de cada PCC;
- Estabelecer as medidas corretivas a serem adotadas quando o monitoramento indicar que os PCCs não estão sob controle;
- Estabelecer os procedimentos de verificação da eficácia do sistema;
- Estabelecer uma forma de registro dos dados.
Esse sistema apresenta como vantagens:
- o seu caráter preventivo;
- a confiança dos consumidores – garante um alimento seguro;
- é aplicável em qualquer indústria;
- é um método científico e racional para a identificação de PCCs;
- é dinâmico e contínuo para a solução de problemas;
- a valorização e aumento da eficiência operacional;
- e a agregação de valor ao produto.
Como desvantagens têm-se o período longo para a implantação, a necessidade de mão de obra qualificada para implementá-lo e realizar a manutenção, o treinamento constante dos operadores se o turn-over for elevado e é aplicável somente em escala industrial ou em alimentação institucional (FORTES, 2002; GONÇALVES, 2011).
O ponto crítico de controle (PCC) é um ponto, etapa ou procedimento no qual o controle pode ser aplicado com o intuito de eliminar, prevenir ou reduzir a níveis aceitáveis os riscos à segurança alimentar (FDA, 2001).
Dessa forma, a análise dos pontos críticos na indústria de laticínios tem importância, pois permite identificar e prevenir a ocorrência de riscos à saúde humana, bem como evitar alterações nos lácteos, através da aplicação de práticas de controle em determinadas etapas da produção, nas quais existe maior probabilidade de ocorrência de perigos ou situações críticas (SPEXOTO, 2003).
Esses pontos são caracterizados como realmente críticos à segurança, sendo que as ações e esforços de controle devem ser concentrados (SENAC/DN, 2001).
5.1 Classificação de PCC’s
PCCs podem ser classificados quanto ao controle exercido sob o perigo de três formas:
- PCCe, quando são eliminados;
- PCCp, quando são prevenidos; e
- PCCr, quando são reduzidos, minimizados ou retardados a níveis significativos (SPEXOTO, 2003; PEREIRA, 2007; HILBIG, 2012).
Também há que se considerar o ponto de controle (PC), o qual é definido como qualquer ponto, etapa ou procedimento no qual o risco pode ser controlado prioritariamente por programas de pré-requisitos (SENAC/DN, 2001).
Segundo a Resolução DIPOA/SDA nº 10 (2003) a Análise de Perigos e Pontos Críticos de Controle (APPCC) é definida como um sistema amplo para a garantia da inocuidade, da qualidade e da integridade do alimento.
Como parte desse programa, é necessário o estudo e a definição dos pontos críticos de controle.
O sistema APPCC envolve o estudo sistemático da produção dos alimentos, incluindo todas as operações que ocorrem desde a obtenção da matéria-prima até o consumo do alimento (SENAC/DN, 2001).
Esse sistema permite identificar, avaliar e controlar os perigos antes que eles ocorram e tem sido reconhecido como o meio mais eficiente e efetivo para assegurar a segurança dos alimentos (CARNEIRO; SOUZA, 2002).
Como identificar os Pontos Críticos de Controle?
A análise dos PCCs inicia com a elaboração do fluxograma, que permite conhecer e descrever o processo de preparo do produto.
A partir do fluxograma de processo, é necessário identificar os perigos que podem ser encontrados em cada etapa e suas respectivas fontes (SENAC/DN, 2001).
Depois de identificados os perigos, inicia o processo para avaliar se ele é um PCC, o qual geralmente é facilitado pelo uso da Árvore de Decisória (AD).
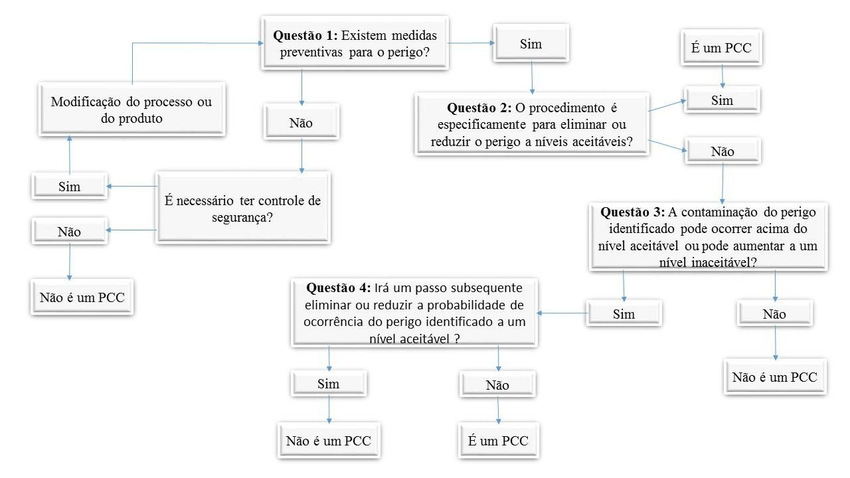
Quadro 1: Exemplo de Árvore Decisória (AD)
A AD é uma sequência lógica de perguntas e respostas, sendo sua aplicação útil para ajudar a determinar se uma etapa específica corresponde a um PCC, PPRO, ou se é um etapa controlada pelo programa de pré-requisitos, para todos os perigos previamente detectado.
Monitoramento dos pontos de riscos: técnicas de amostragem
Os pontos de risco em uma indústria também podem ser identificados a partir da coleta de amostras e a sua análise.
Para isso, o MAPA definiu parâmetros microbiológicos e físico-químicos tanto para a matéria-prima quanto para os produtos finais, que ajudam a atestar a qualidade do processo de produção (BRASIL 2011, 2016).
Os equipamentos, manipuladores e o ambiente também podem ser monitorados por meio de coleta de amostras para análises microbiológicas.
As análises microbiológicas podem ser realizadas com as técnicas convencionais – como a contagem padrão em placas, placas Petrifilm®, inoculação em tubos múltiplos, ATP-bioluminescência – ou por avançadas técnicas moleculares, como a reação em cadeia de polimerase (PCR) e o sequenciamento de DNA em larga escala.
Sequenciamento de DNA em larga escala no mapeamento de pontos de riscos
Com as metodologias tradicionais de análise microbiológica não é possível ter escala e especificidade ao mesmo tempo, ao analisar pontos de riscos.
Para analisar o crescimento total de bactérias ou fungos, utilizamos meios genéricos que permitem o desenvolvimento de microrganismos em condições de apropriadas de desenvolvimento.
Porém, perdemos especificidade e não conseguimos identificar quais são os microrganismos que estão se desenvolvendo, se são deteriorantes ou patogênicos, se possuem maior ou menor capacidade de gerar biofilme, se são termorresistentes, entre outros.
Por outro lado, se usamos meios específicos para identificar espécies mais relevantes para o mapeamento de pontos críticos, perdemos escala e precisamos direcionar para uma ou duas espécies.
O sequenciamento em larga escala vem mudando esse paradigma ao permitir a identificação de microrganismos com especificidade e escalabilidade a um custo acessível.
Utilizando marcadores molecular universais, como o gene 16S rRNA para bactérias e ITS para fungos, é possível identificar e quantificar toda a microflora presente em uma amostra.
Essa abordagem é feita em algumas etapas que envolvem a extração e purificação do DNA, preparo de bibliotecas, sequenciamento do DNA das amostras e análises de bioinformática.
Algumas empresas como a Neoprospecta, já disponibilizam essa abordagem no Brasil.
O monitoramento microbiológico: Plataforma Neobiome
O monitoramento microbiológico pode indicar pontos de riscos em uma indústria de lacticínio e auxiliar na prevenção e gerenciamento de riscos.
O conhecimento dos pontos críticos da produção permite aplicar medidas corretivas e preventivas de forma eficiente para mitigar ou eliminar as contaminações.
A plataforma Neobiome é uma ferramenta de gestão e mapeamento de riscos a partir de informações do microbioma. Essa plataforma associa o Diagnóstico Microbiológico Digital (DMD), método que utiliza como base o sequenciamento de DNA em larga escala, a um software, gerando informações que permitem a rastreabilidade de agentes biológicos e o mapeamento em todas as etapas da linha de produção.
Os diferenciais do uso dessa tecnologia são:
- a visualização didática e interativa dos resultados microbiológicos;
- a identificação dos micro-organismos em larga escala;
- os diagnósticos com alta sensibilidade, especificidade e precisão;
- a transformação de informações imateriais em conhecimento concreto para a tomada de decisão;
- e o baixo custo (NEOPROSPECTA).
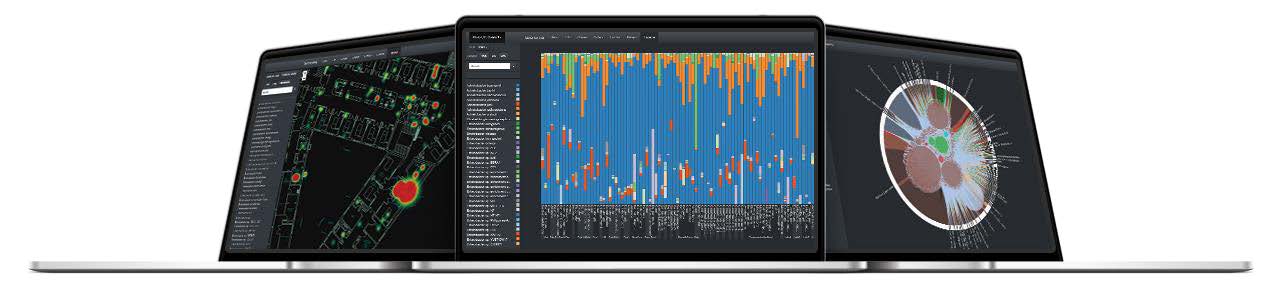
Quadro 2: Plataforma Neobiome – Neoprospecta
O monitoramento microbiológico: Mapa de risco
O software Neobiome gera conhecimento a partir de informações microbiológicas. Por meio de um algoritmo que calcula padrões de riscos, é possível identificar visualmente os pontos de risco em uma planta baixa, mostrados em forma de mapa de calor.
Com essa ferramenta, fica mais fácil ver quais os pontos da indústria possuem maiores concentrações de microrganismos patogênicos ou deteriorantes e onde estão localizados os pontos críticos e as falhas de processos.
Desse modo, as correções nos processos podem ser feitas de forma rápida, assertiva e direcionada.
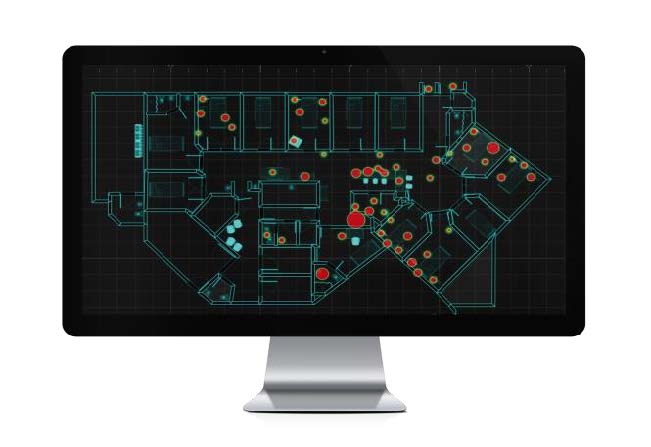
Quadro 3: Mapa de Risco indicando pontos de contaminação.
Independente da metodologia adotada, o fundamental é implementar um plano de gestão de riscos, definir os pontos críticos de controle e mapear os principais riscos na indústria de laticínio, a fim de evitar danos à saúde do consumidor e prejuízos à instituição.